CHRYSTAL PLASTIC – Full focus on sustainability
Partner-Story with PBH France
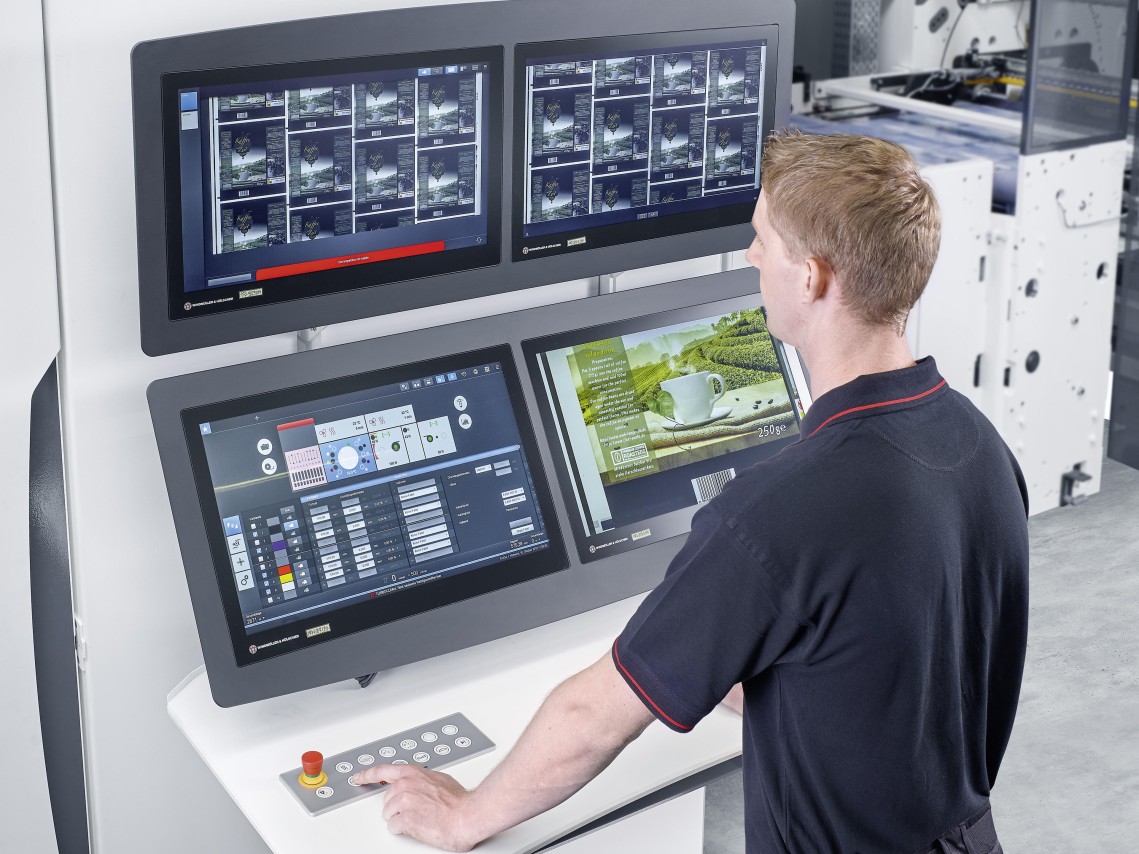
As a long-standing customer of WINDMÖLLER & HÖLSCHER, CHRYSTAL PLASTIC has just placed an order for a 10-colour printing press and a blown film extrusion line. This order, which is being supported by PBH France, W&H's long-standing partner, is part of an investment by CHRYSTAL PLASTIC that aims to make production more resource-efficient and to focus on recycling.
About CHRYSTAL PLASTIC
CHRYSTAL PLASTIC, a family business run by Éric Dufour and his two sons Augustin and Clément, has four production sites, the two most important of which are located in Caudry (North). One site is dedicated to extrusion and printing for the aerospace, automotive and construction industries; the other to extrusion, bag production and printing for the food industry. In 2020, the company received BRC certification with an AA rating for this second location.
With the support of PBH France, CHRYSTAL PLASTIC has been investing in WINDMÖLLER & HÖLSCHER machines for several years. After the first purchase of an OPTIMEX 3-layer extrusion line in 2016, the company again placed an order for a MIRAFLEX flexographic printing press and an OPTIMEX 3-layer blown film extrusion line in 2019 and 2020. As part of the cooperation, PBH France was able to advise the management team of CHRYSTAL PLASTIC, support them in the selection of the machines, as well as support the installation and commissioning. Éric Dufour testifies: "We have established a relationship of trust with PBH,; They understand what is important to us. In addition, we can count on the technicians from WINDMÖLLER & HÖLSCHER to support us remotely or even on site if necessary."
Last January, CHRYSTAL PLASTIC started a new investment to equip itself with a 10-color NOVOFLEX II flexo press with a print width of 1,650 mm (5.41 ft) and a 5-layer VAREX II blown film extrusion line with a width of 2,800 mm (9.19 ft). This expansion of production gives CHRYSTAL PLASTIC the opportunity to respond to the specific needs of the food market, which is particularly demanding in regard to technical films and environmentally-friendly solutions.
CHRYSTAL PLASTIC has been committed to this path for a long time. They have already established a system for collecting production residues from customers (most of them within a radius of 200 km) for subsequent treatment and recycling on the extrusion lines. The recycled content can be up to 80% of the production. "We have just received the ECOVADIS bronze medal at the end of 2021. This year we hope for the gold medal! " announces Éric Dufour.
In order to respect the environment, but also the working conditions of its employees, CHRYSTAL PLASTIC has opted for fully automatic machines.
The NOVOFLEX II was introduced with a print width of 1,650 mm (5.41 ft) in 2020 and is equipped with with many assistance systems:
- VISION inspection system for web monitoring and defect detection
- Sleeve handling system NOVOPORT M for easier handling of anilox roller sleeves, format sleeves and adapters
- COREMATIC system, which automates the unloading of the rollers and the feeding of the cores
Éric Dufour adds: "The NOVOFLEX II is a very efficient machine that will allow us to work on large print formats (e.g. mineral water) by producing twice as much with the same energy consumption and reducing our waste rate. The machine is also very convenient to operate for our technicians."
The VAREX II, equipped with the latest TURBOSTART module, a start-up assistance system and Filmatic II N winders, enables the production of rolls with excellent flatness. Éric Dufour: "This extrusion line will allow us to respond to the increasing demand from major customers for recyclable products made from recycled materials".
This collaboration between PBH, CHRYSTAL PLASTIC, and W&H, promises to flourish with 2023 commissioning as the next steps. Stay tuned.