When an invention develops into the national standard
More than 26 years after patenting the first machine for PP block bottom valve sacks W&H still holds the technological leadership with record production of 140 sacks per minutes.
26 years ago, German machine builder Windmöller & Hölscher invented and patented the technology to create hot air sealed block bottom sacks made of woven PP. Today, China has made this sack concept one of three national standards for cement packaging by mid-2022. Since inventing the first machine, W&H has advanced the technology, building on years of experience with industrial sacks. Today over 500 CONVERTEX are in use worldwide. The newest generation of them produces 140 sacks per minute at highest quality levels representing the technological leadership in this type of equipment.
“The first CONVERTEX was shipped to customers in 1996 and produced 40 sacks per minute” remembers Walter Haeder, Division Head of Woven PP Machinery. Today the product range features machines with capacities of 100, 120 and 140 sacks per minute. To cope with the ever-increasing demand on volume and productivity, Windmöller & Hölscher continues to invest in further enhancing the technology to new productivity levels while reducing the carbon footprint through reduced energy consumption of the machines and most of all by lighter and stronger sacks.
“W&H not only offers machinery for woven pp sacks, but also for industrial sacks made of paper and film”, explains Haeder. W&H invented the first machines to produce industrial paper sacks in the 1920s and for pasted plastic sacks in the sixties. Alle three sack concepts profit from common technology – for example block bottom technologies were first developed for paper sacks and then led to the patent of the first machine to create the block bottom PP woven valve sack by W&H – the basis for all machines that now produce the required type of woven PP sacks. “Our expertise in all materials for industrial sacks gives us unique insights, especially now when one sack concept has to be replaced with the other”, explains Haeder.
China is the largest cement market in the world and almost half of the consumption is packed in sacks. So far, the predominant sack concept was a simple sewn wPP sack. This packing has several drawbacks of which the loss of cement during handling and transport is most disadvantageous. This loss of cement causes air pollution and significant additional carbondioxide emissions because the depletion is not reaching its planned use and must be replaced. The new national standard calls for the improved sack concept for which W&H developed the technology and the Chinese investment in clean air and reduced carbon footprint is greatly supported by the CONVERTEX supplied by W&H.
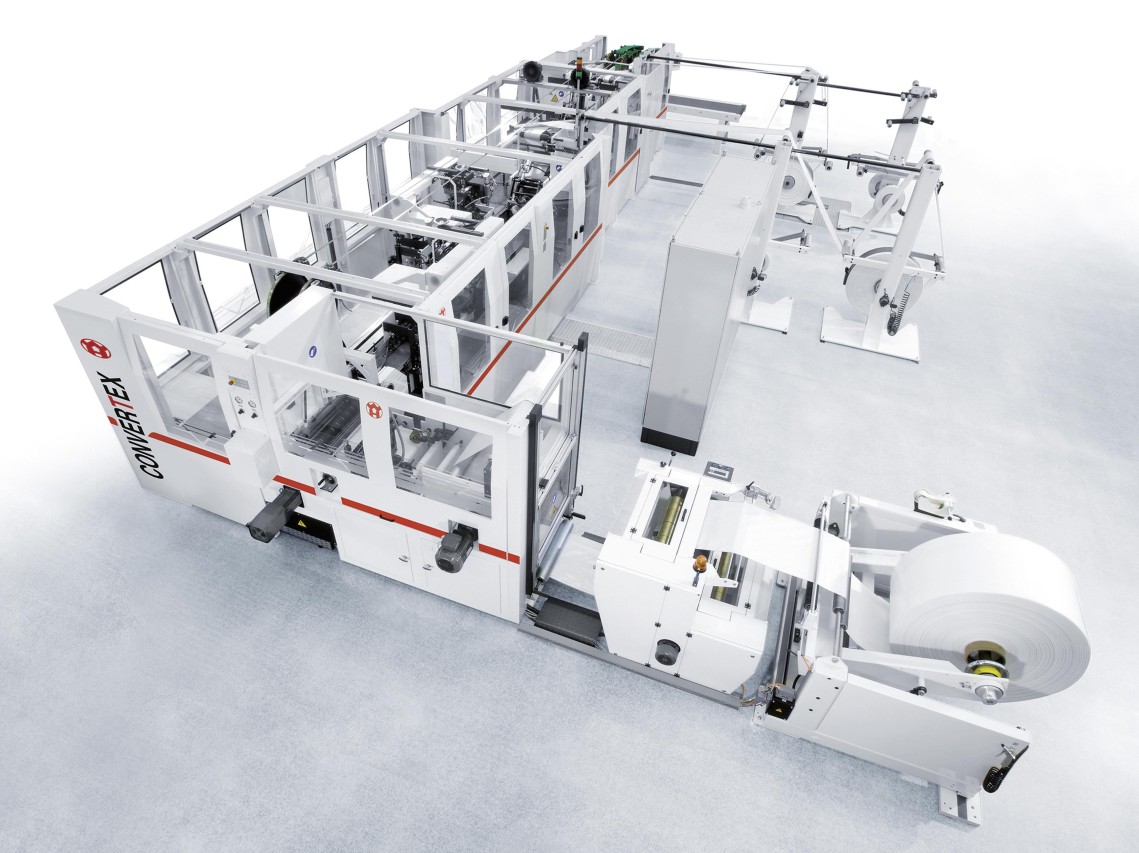