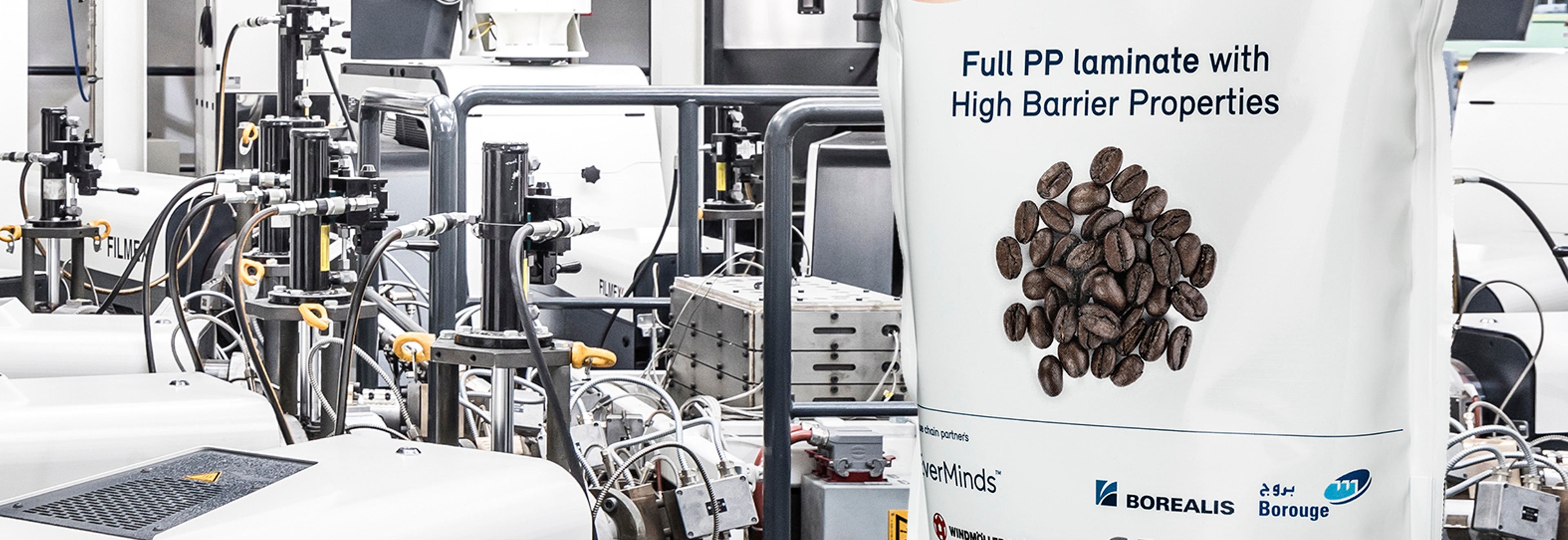
Extrusion
Full PP Pouch with high barrier properties
PP based laminate designed for recyclability with barrier characteristics
Get in touchYour benefits at a glance
One Pager
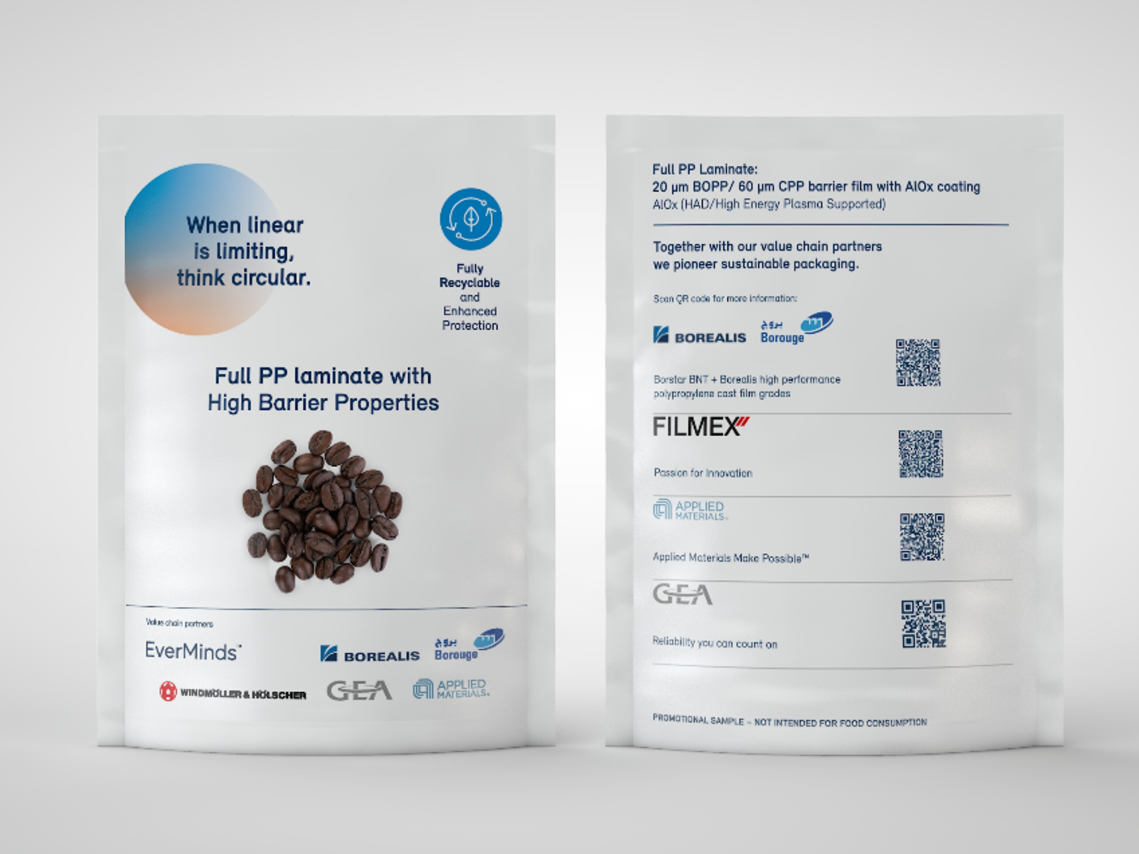
All about Full PP Pouches with high Barrier Properties
Barrier films are established firmly in our modern world for protecting foodstuff and other goods. Their possibility of being specifically tailored to the use is unmatched by paper, glass or metal. Further their low weight contributes to lowest energy consumption during transportation and makes them eco-friendly compared to the other packaging solutions. However the sustainability of plastics in general is still a big point of criticism.
Amongst missing waste management systems, many of today’s barrier film compositions are not suitable for being recycled for a second life in packaging. Typically their multilayer structure consists of several inseparable raw materials and hence cannot easily be processed to regrind, which may be used within a subsequent lifecycle. This has to be changed and we as leading supplier for cast film machines are happy to provide support to improve packaging solutions towards more sustainability.
With the FILMEX II cast line film structures can be processed flexibly. At the same time they can be designed to comply with the need for maximum recyclability. The pouch made of a full PP laminate with high barrier properties is a design example for a sustainable packaging application. A base film structure mainly containing polypropylene with a minimized usage of high barrier raw materials ensures that design requirements for recyclability are met. An additional inorganic coating on the base film provides additional enhancement of the barrier properties without adding noteworthy amounts of extraneous material. By that oxygen transmission rates (OTR, 23°C/50% RH) below 1 may be achieved. Finally the barrier film was laminated with a counter printed PP based film to consequently follow the idea of using only one material for better sustainability.
- Barrier properties adjustable by incorporation of high barrier resins, as well as by applying thin inorganic coatings
- Excellent optical and mechanical properties delivered by a highly efficient cast film process
- Most consistent film quality with superb layer distribution for thinnest barrier layers
Our Partners
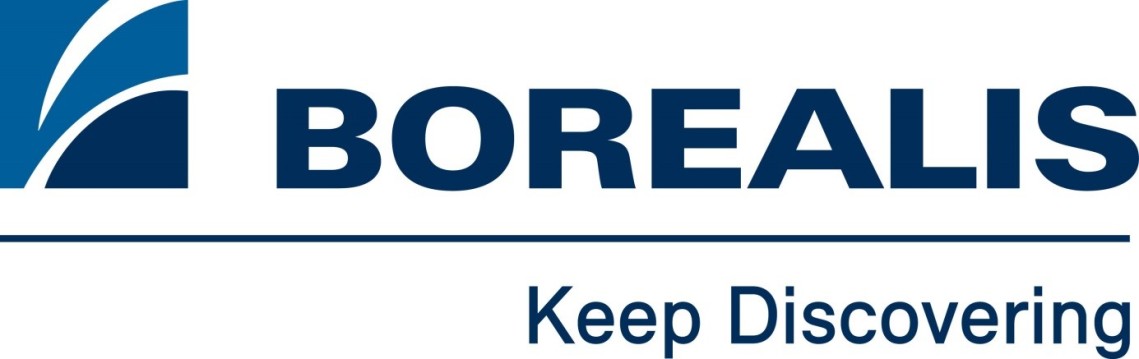
Borealis
With over 50 years' experience in the industry, Borealis is an innovative and reliable supplier of superior polyolefin plastic materials used in consumer products, advanced packaging and fibre.
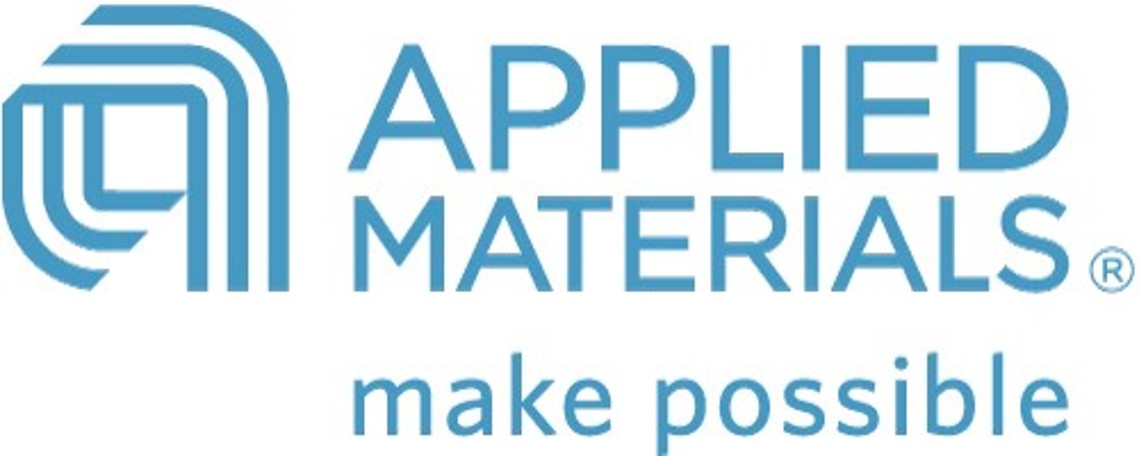
AMAT
Applied Materials, with more than 60 years of experience and >700 installed systems, is the leading supplier of advanced roll-to-roll vacuum coating-systems. Our dedicated production platforms are used for deposition of thin films for touch panels, flexible electronics and displays, packaging and advanced technology applications.
About Sustainability
Sustainability is an important purchase criterion for end consumers today. Manufacturers of flexible packaging face the challenge of developing sustainable packaging solutions while also managing their production processes as sustainably as possible.
The FULL PP Pouch with high barrier properties is an example for approaching design solutions flexibly on a modern cast film line, which offers highest efficiency and process consistency.
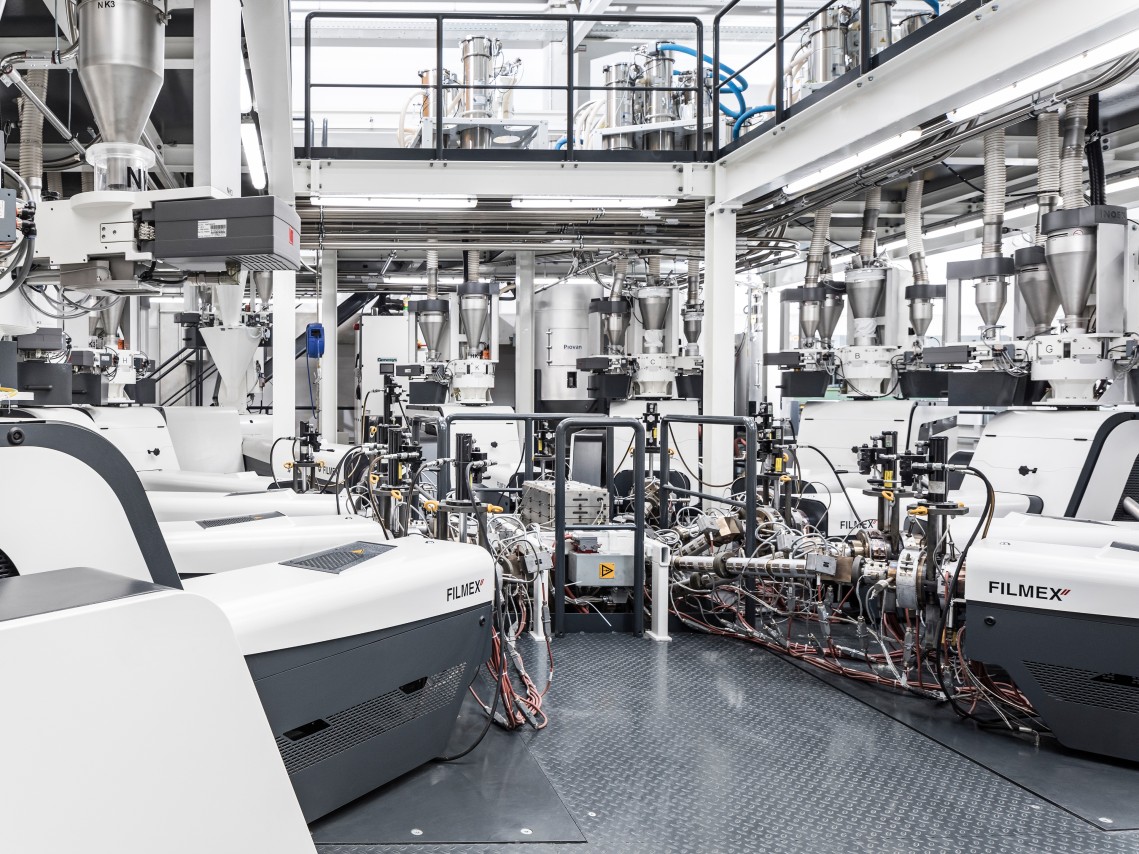
Why FILMEX II
The FILMEX II is based on a modular concept that enables optimal user- and product-specific configuration options, thus offering the greatest possible flexibility in product design. The development of the FILMEX II was driven by productivity, flexibility, automation and sustainability. Every component is designed to deliver consistent, superior quality film at top outputs.
Short start-up and changeover times reduce the use of raw materials and significantly decrease the amount of waste – while maintaining convincing film quality. The unique W&H screw design guarantees consistent and perfect melt quality. Feedblock, die and chill roll unit are seamlessly matched to each other and allow for optimum solutions when producing mono, multi-layer or nanolayer films.
The FILMEX II is equipped with fully integrated automation. The user-friendly, intuitive PROCONTROL TS user interface covers all machine components – from pellet supply to winder.
- FILMEX II individually customizable to your specific customer requirements as a result of modular concept
- FILMEX unique screw design provides excellent melt quality for all types of resins
- Precise and reliable resin dosing ensures excellent single layer precision
- FILMATIC (TC II) and FILMATIC PS winding technology ensures superior reel quality for best downstream processing