Smart handling of claims
How RUBY Go increases transparency in production and helps to save costs in the management of claims.
Since the foundation of the austrian company G. Coreth Kunststoffverarbeitungs GmbH in 1980, they developed from a producer of construction film, tubular film and bags to a big player in film production. Today Coreth manufactures approximately 33,000 tons of film per year in four-shift operation (24/7) on 54,000 square metres. Inbetween Coreth opened a centre for the production of superior-quality printed film to complete the range of customized packaging solutions. The cornerstones of their philosophy are high service orientation, continuous innovation and competent staff. Coreth is consistently applying their quality standards on a daily basis.
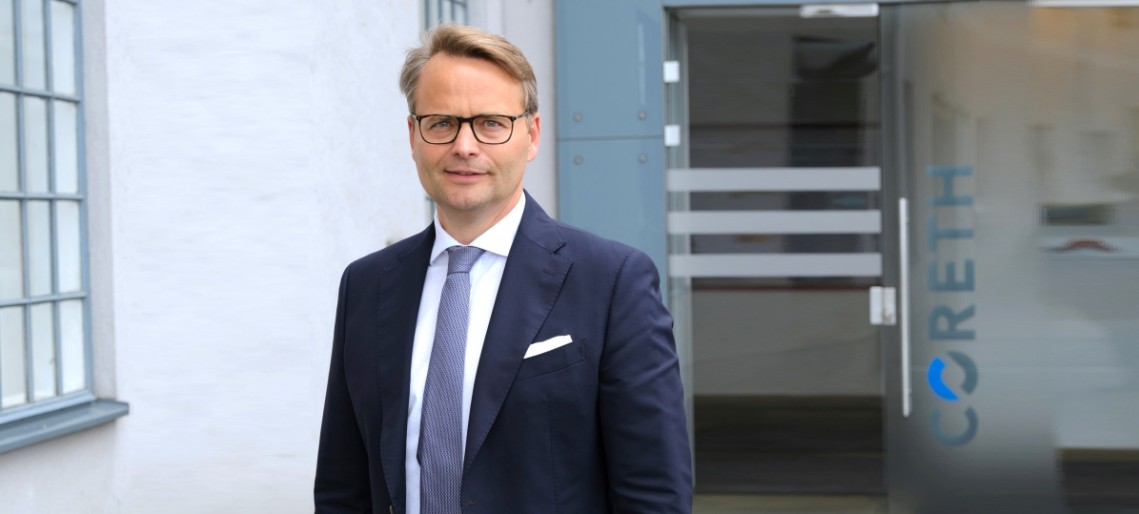
Gain transparency over production
With Coreth there is a longterm business relationship since 2008. In 2021, Coreth and W&H initiated a collaboration in terms of the IoT system RUBY
in order to gain transparency over the production. As a starting point, RUBY records the data from one extrusion machine. RUBY Go helps to digitize their production and the value chain. Within the IoT system it is possible to check if all adjustments have been made correctly. Machine settings can be stored within RUBY and retrieved for upcoming orders. Coreth monitors if there are deviations between the planned and real values within the production as for example in the throughput. By this opportunity for comparison the overall claim rate has been reduced significantly.
Save costs in the management of claim
RUBY enables the user to store the production data longterm. In the case a claim occurs Coreth has the possibility to analyse production data of the longer past. This already gave big advantage to Coreth as Stefan Chalupnik, Managing Director of G. Coreth Kunststoffverarbeitungs GmbH, quoted: „RUBY has already saved us a lot of costs! One example is a claim about a large delivery and the selection of three faulty rolls from a total of 48. As a result, the rest could be processed by the customer without any problems and without further disruptions.“
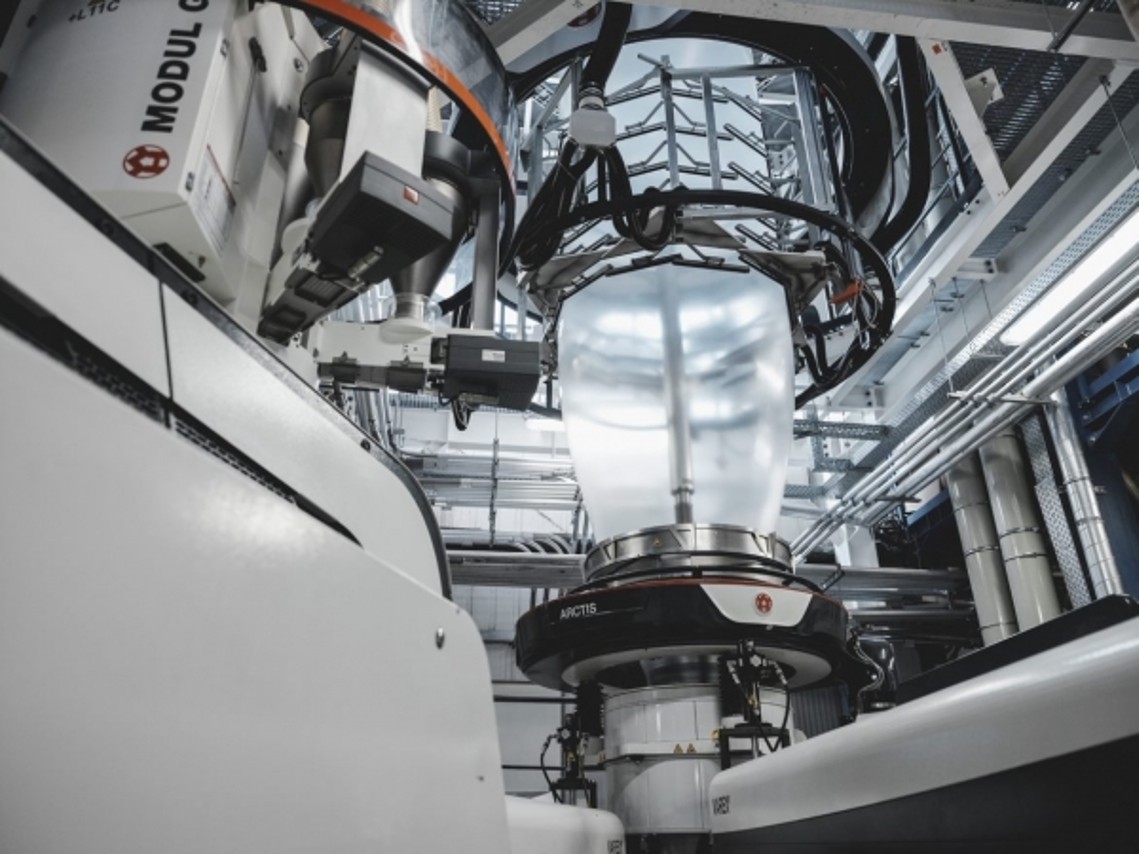
RUBY Training increases certainty
W&H also offers trainings in order to give praxis-oriented tips and tricks on defined learning concepts and with clear learning objectives. To take full advantage of RUBY and the W&H machine, some Coreth employees have been trained to use the job level and recipe memory on the machine. This helps to improve the quality of data and simplifies the analysis with the IoT system. Stefan Chalupnik said: „With the training we could increase confidence in the use of our machines. This leads to less mistakes. Herewith W&H could prove once again that it is not only important to produce excellent machines. Also service and consistantly good consulting are relevant success factors for a fruitful partnership.“
Continue the collaboration for more output
Coreth and W&H will continue their good collaboration in the future and work on further common topics.