Die Head Service: Convincing quality & performance
EK-Pack appreciates the hassle-free package from the initial contact to the final documentation.

Serving ambitious markets with innovation
As a specialist in the production of high-quality films for the food, non-food, pharmaceutical and medical industries, EK-Pack Folien GmbH produces modern film structures on various blown, cast and laminating film lines. 210 employees work in the company, which was founded in 1977 and has been a part of the Oliver Healthcare Packaging Group since June 2023, with the aim of serving ambitious markets with innovative film systems. Under the guiding principle of “Flexibles for Recycling”, there is a focus on developing customer-specific solutions for resource-efficient and environmentally friendly film structures.
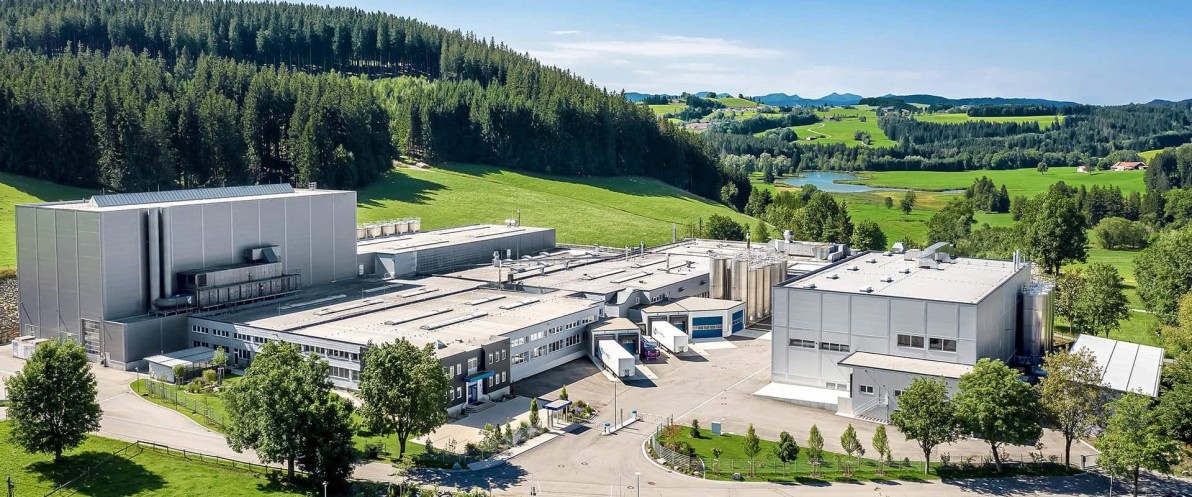
Highly valued partnership with W&H
To meet market challenges and deliver high-quality products quickly, EK-Pack places great importance on maintaining a flawless machine park. This also includes keeping the die head, the heart of the machine, in top condition. So it is not surprising that the company has always opted for professional die head cleaning. Since 2013 when the company acquired its first VAREX 9-layer blown film line from W&H, the film manufacturer has relied on W&H‘sprofessional service, which has consistently met their expectations.
Dirk Kuchheuser-Bierhals, Head of Die Head Service at W&H, reports: “We started cleaning the 5-layer die head from another manufacturer for EK-Pack in 2013. Since then, EK-Pack has had its die heads cleaned and inspected by us every year.” Various die heads have passed through our professional service over the past decade, including W&H‘s 3-layer and 9-layer die heads, as well as those from other manufacturers. Most recently, the feed block of the FILMEX II cast film line was cleaned by experts at W&H‘s headquarters. The processing times ranged from five to eleven working days, depending on the size of the die head. “We appreciate working with W&H. Our interactions are open, honest, and respectful, almost familial. Finally, we receive comprehensive documentation with reports and images. Everything you need to make the right decisions,” concludes Peter Stober, Managing Director Operations of EK-Pack.
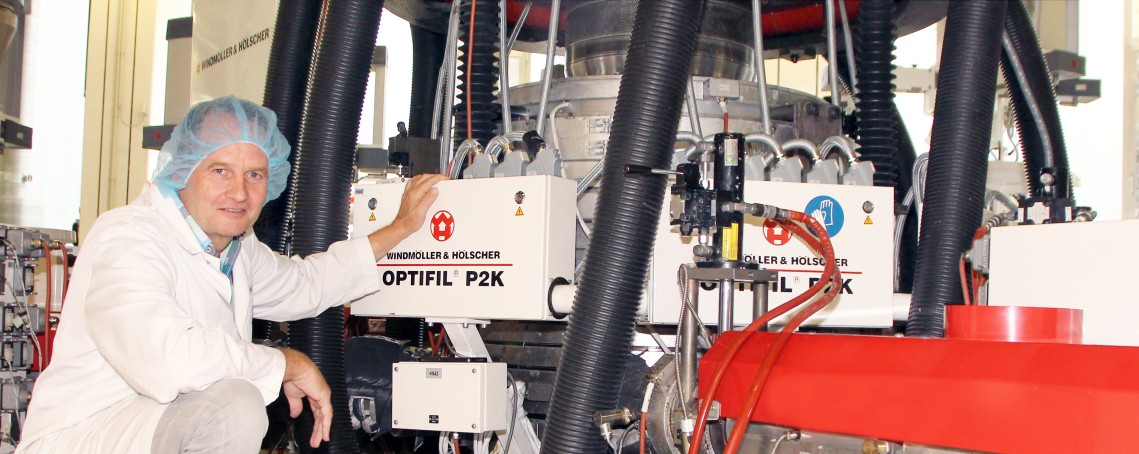
Successful overhaul of the 9-layer die head
With a strong foundation of trust built through previous projects, W&H was entrusted with the task of overhauling the 9-layer die head. Stober reports, “W&H impressed us with their excellent work, reliable processes, and comprehensive, transparent communication. Additionally, the company is highly flexible: When things get tight, and we have short-term needs, we always find a solution together. So, we didn‘t hesitate to entrust W&H with the significant challenge of overhauling the die head.” In the course of this project, both companies collaborated to find a solution. The overhaul, including a new coating, was well-prepared to minimize downtime. Not least because the VAREX at EK-Pack runs 24/7. W&H had a 9-layer die head built for rental that closely matched EK-Pack‘s configuration and also served as a suitable rental die head for other customers. Stober was highly satisfied with the service: “In the end, we had almost no production downtime. The few film widths that could not be produced on the rental line during the 17-week overhaul we were able to produce elsewhere thanks to well thought-out planning. Now our die head is as good as new. It was put back into operation smoothly and on schedule. W&H gave us the assurance that it would work, and they delivered on that promise. The ratio between price, quality and performance is right here.”
A look into the future
In the future, EK-Pack plans to continue to entrust W&H with the heart of its extrusion lines. Stober summarizes, “The professional die head service offers a hassle-free package from the initial contact to the final documentation.”