Relocation for a quick restart of production
How our one-stop solution for machine relocation convinced our customer ATE Plast OOD.
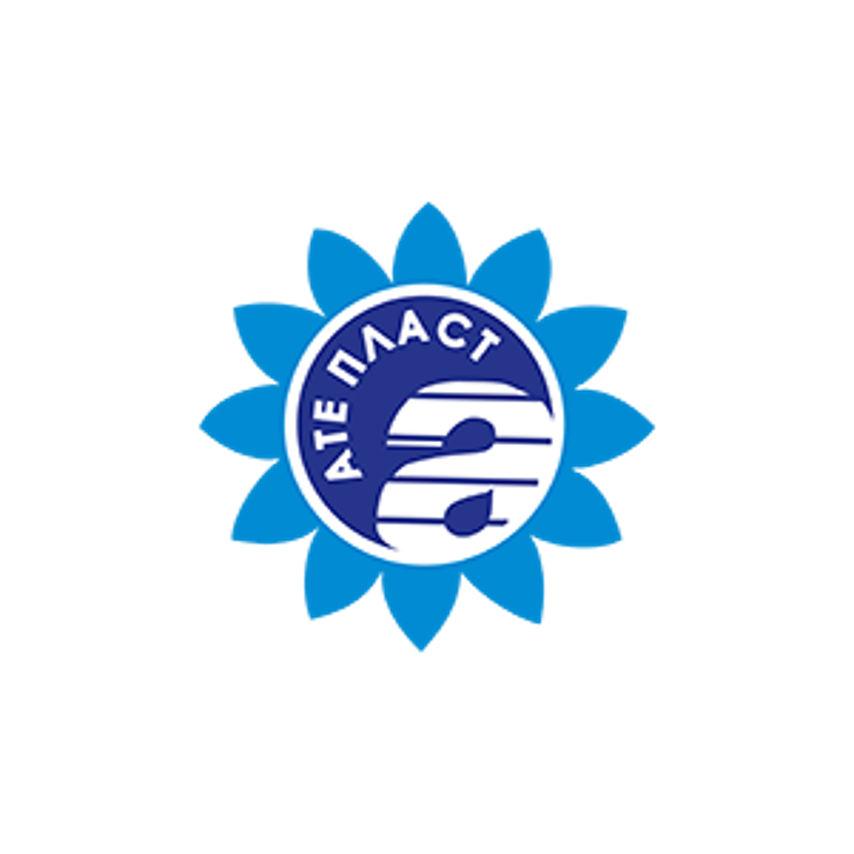
Focused on innovations and leading trends
ATE Plast OOD, a family-owned company with nearly 30 years of experience, is a leading manufacturer of high-quality PE films and packaging in Bulgaria. Their products are distributed in over 30 countries to more than 1,000 customers, emphasizing innovation and modern packaging solutions. With two production plants, they operate mono- and multilayer blown film lines, advanced flexo printing, laminating machines, and various converting equipment. They produce 14,000 tons/year of film and 4,000 tons/year of printed and laminated packaging. ATE Plast has been a long-term customer of W&H. The first machine, a VAREX 3-layer extrusion line, was delivered in 2008, others followed. In 2023, the company had built on a greenfield site the largest and most modern printing plant in Bulgaria. One part of this big project was the relocation of their MIRAFLEX from the existing production facility to the new built plant.
A large project with several challenges
“At the beginning of the project we had to decide how to organize the relocation of the MIRAFLEX in order to move as quickly as possible and to ensure at least the same machine condition and print quality after the installation of the press in the new plant,“ reports Ivo Zhekov, Shareholder and Financial Director/CFO at ATE Plast OOD. Due to the high level of trust in W&H, the machines and the excellent service, the customer decided to entrust W&H with this responsible task: “We appreciate the quality of W&H, the modern, innovative machines and also the technical services. The machines have a good level of automation and each new generation is better than the previous one. We also like the way how W&H is implementing the Industry 4.0 technologies in the new machines,” states Zhekov.
W&H offered a one-stop solution, including project planning and development of a holistic relocation concept. W&H did a process check on the machine at the old location in order to define the status of the MIRAFLEX as a guideline for the same job at the new location. In addition to this an inspection has been done with recommendation for spare parts, following by the safe dismantling and supervision of packaging. The transport has been arranged by the customer. At the end, W&H carried out the assembly and commissioning of the machine at the new location. To complete the project with the customer‘s approval after 8.5 weeks, the same job was printed at the new location, demonstrating the success of the relocation project.
Zhekov sums up: “Every detail of the move, from disassembly, loading and transport to unloading, assembly and commissioning, was carried out precisely and on time. We will highly recommend W&H as a partner for relocation of machines. Thanks to the realization as a partner project we did not have to hire additional staff and could keep the time of our maintenance technicians for our running machines. In the end, it saves time and additional costs, so W&H‘s relocation service was a wise investment.”
For the future, W&H and ATE Plast are working on further projects in order to continue the good business relationship.