Defect detection and analysis made easy
How RUBY helps in documentation to fulfill certifications and other customer requirements
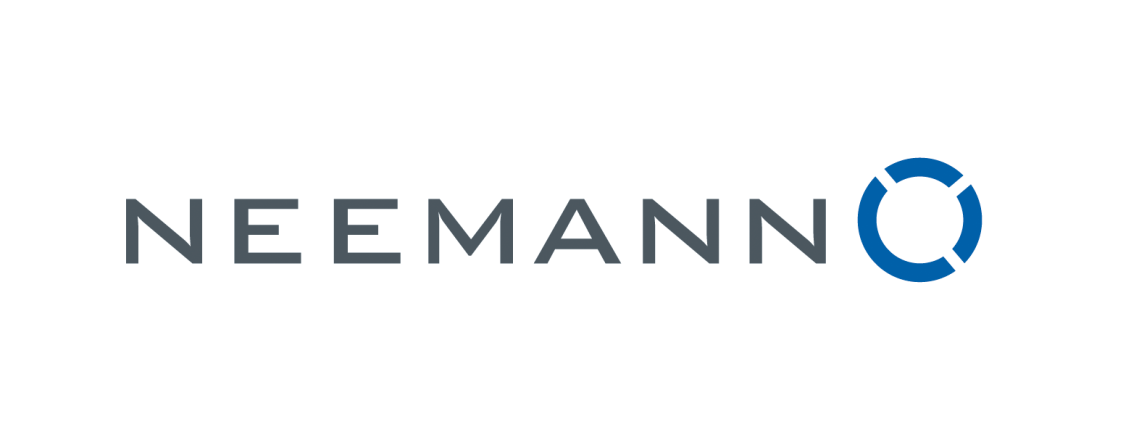
RUBY as a decisive instrument for documenting quality and hygiene specifications
The company NEEMANN LiteFlexPACKAGING (M. Neemann OHG) looks back on a long history of 133 years in the flexible packaging market. The family-owned company generated sales of more than 50 million euros in 2022, primarily with FFS films for the food and non-food sector and pouches for the hygiene industry. NEEMANN has relied on Windmöller & Hölscher since 1946. Today, their machine park includes several W&H printing presses. In the extrusion sector, the company produces on a VAREX blown film line, among other things. The products are part of primary packaging for consumer goods, which have to fulfill functional and communicative tasks. Ensuring and documenting customer specifications in accordance with the required norms and standards is therefore an essential part of their daily work. Great attention is paid to product quality and hygiene. In order to meet the increasing requirements, NEEMANN has been relying on the W&H IoT system RUBY since 2020. Wilfried Hoppen, Manager Engineering at NEEMANN, reports: "RUBY is an excellent source of data from which we can derive information: for controlling the company, for documentation requirementsas part of our numerous certifications, for transparency and optimization in our supply chains.“
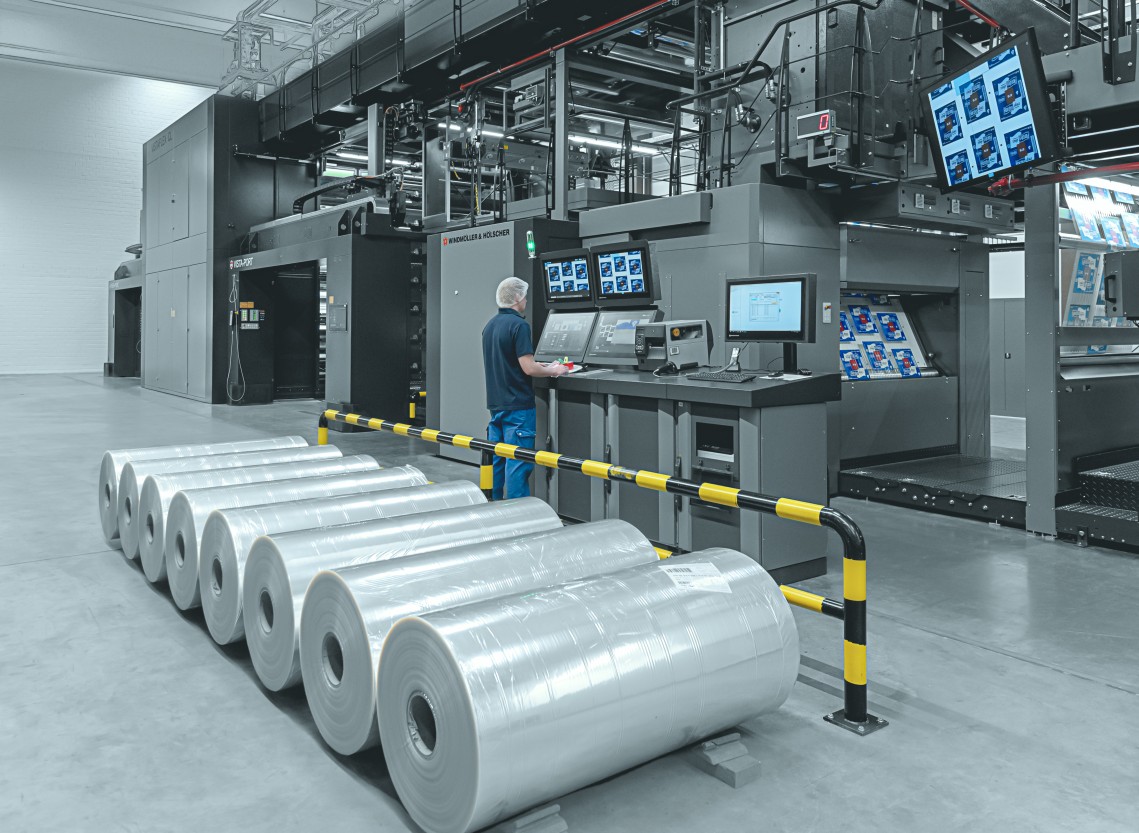
Save time and money with RUBY Check and VISION
The starting point was the introduction of the IoT system RUBY Go and training on it. For some time now, the company has also been relying on the extension RUBY Check. In combination with W&H‘s own inspection system VISION, the software really comes into its own. Marco Kleemann, Manager Flexoprinting at NEEMANN, summarizes: "With RUBY Go and RUBY Check, we save an enormous amount of time and money in the context of defect detection and analysis. Thanks to the VISION system, printing defects are easily identified. The complete storage of printing results allows us to identify and locate defects down to the last meter. This enables us to achieve optimal visibility, reliability and cost efficiency in our supply chain.“
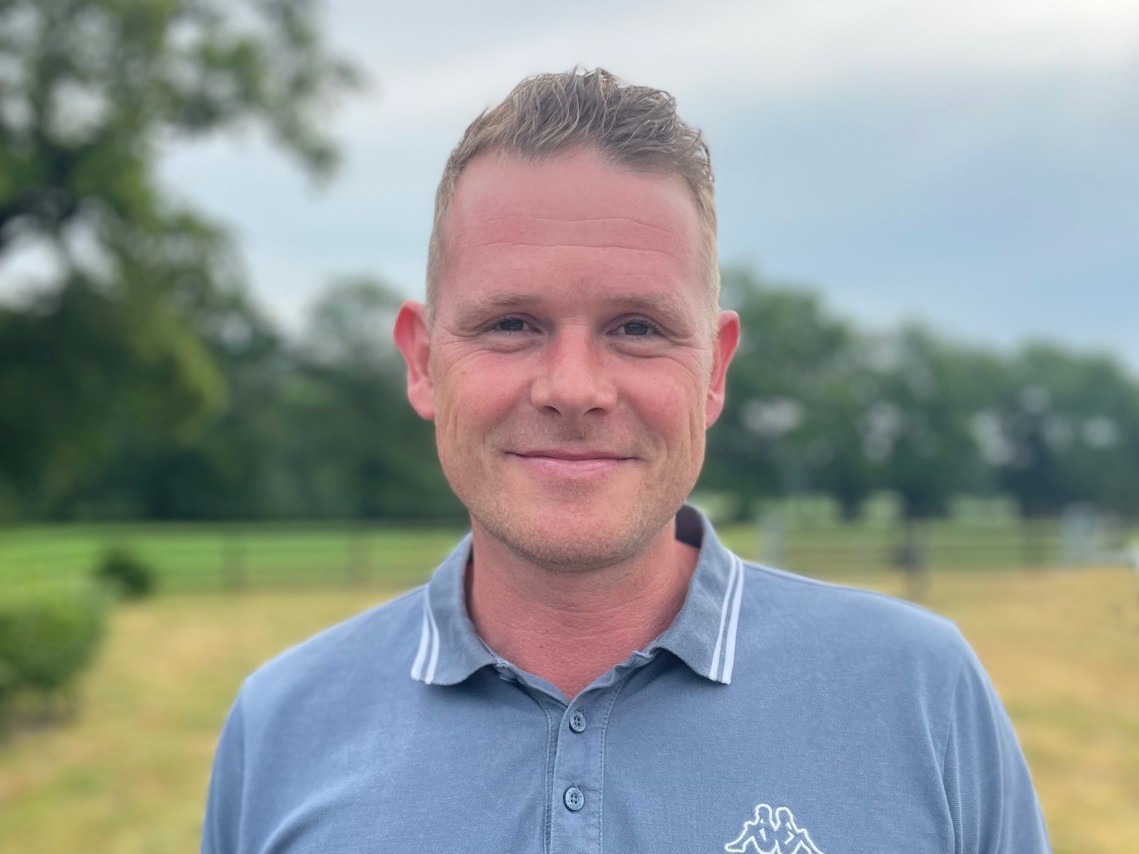
Reduce maculation and downtime
The benefits in the analysis of defects are also enormous, sums up Kleemann: "Thanks to RUBY we can review and evaluate machine settings afterwards. We define causes of defects and avoid them in following orders. RUBY enables us to look at different parameters in interaction over a longer period of time, e.g. web tensions in connection with recognizable deviations in the print. From this, we derive measures such as the proactive replacement of wear parts to reduce downtime. Additionally we have already detected defects in machine operation through RUBY and thus minimized waste in following orders.“
Fit for the future thanks to RUBY App and optimized energy monitoring
In the next step, NEEMANN would like to begin using the RUBY App. This allows the Manager Flexoprinting to keep an eye on the production and get answers to important questions while on the move: "Is the printing press operating, which job is currently running and how fast?“ At NEEMANN, RUBY also plays a role in providing energy-related data. Together with W&H, the company would like to work on using RUBY to optimize their energy monitoring in a second step. The aim here is to find out how much more efficiently one machine runs compared to another and why. NEEMANN is additionally considering to connect the VAREX blown film line to RUBY in order to take advantage of the IoT system also in extrusion business.